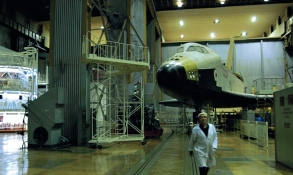
Неужели россияне разучились работать? Такой горький вывод делают сегодня некоторые эксперты, сравнивая уровень производительности труда у нас и в США: более чем шестикратное отставание! Но дело не в лени – сильнейшим тормозом является изношенное, морально и физически устаревшее оборудование, на котором, как ни старайся, многого не достигнешь. Его давно пора сдать в утиль…
Вообще-то мы и сто лет назад, сравнивая соотношение производительности труда в нашей стране и в США, сильно расстраивались. Царская Россия отставала по этому показателю от Америки в 9 раз (данные за 1913 год). Но после Октябрьской революции столь фатальный разрыв начал сокращаться. Особенно ощутимых результатов удалось добиться во второй половине прошлого века. Технику для предприятий разрабатывали отечественные научно-исследовательские, проектные институты, конструкторские бюро. Страна закупала немало станков за рубежом (особенно с начала 60-х годов, когда в СССР устремился первый поток нефтедолларов). А новейшую электронику, продавать которую Советам американские фирмы не имели права, наши внешнеторговые организации приобретали через третьи страны. В результате в 1988-м СССР уже не в 9 раз, а только вдвое уступал Соединенным Штатам по производительности труда в промышленности. Тоже, прямо скажем, разрыв немалый, но тенденция по его сокращению была налицо. Конечно, новые технологии использовались большей частью в военно-промышленном комплексе (тогда экономика, как известно, в первую очередь работала на военных). Тем не менее мы показали миру, что умеем трудиться. Причем не только догоняли, но и кое-где (например, в космонавтике) опередили Америку.
Однако за последние два десятилетия Россия по производительности труда вновь стремительно откатилась назад. Шокирующие цифры представило недавно Министерство экономического развития: «По производству добавленной стоимости на одного занятого (проще говоря, по производительности труда. – В.Г.) Россия отстает от США в 5,9 раза; от стран G7 – в 5,2 раза; от Японии – в 4,3 раза». Страны G7 – это Германия, США, Италия, Франция, Великобритания, Япония и Канада. Если же взять выпуск продукции за один отработанный час, то разрыв с США оказывается еще выше – 6,1 раза.
Цифры эти подтверждаются и конкретными примерами. Скажем, в расчете на одного рабочего наша автомобильная промышленность выпускает в 4 раза меньше автомобилей, чем заводы Евросоюза. В Южной Корее на производство одной тонны конструкции в судостроительной промышленности уходит в 3 раза меньше рабочего времени, чем на российских заводах. Не в нашу пользу и сравнение предприятий, выпускающих железнодорожную технику: в России годовая выработка (в долларах) на одного занятого в 8 раз меньше, чем в Канаде…
Наша реальная экономика, как видим, провалилась в глубокую яму. Почему? Что произошло? Может, и в самом деле в условиях экономической свободы россияне вконец обленились, может, они вообще способны трудиться только из-под палки? Такие выводы время от времени приходится слышать из уст апологетов либеральной экономической мысли, утверждающих, что государство избаловало своих граждан неустанной заботой и социальными выплатами.
В цехах космического завода – оборудование позавчерашнего дня
– Работают наши граждане сегодня нередко даже больше, чем раньше, однако сильнейшим тормозом является изношенное, морально и физически устаревшее оборудование, на котором, как ни старайся, многого не достигнешь, – говорит один из организаторов космической и станкоинструментальной промышленности Борис Бальмонт(в 1970-е годы он был первым заместителем министра в ракетном Минобщемаше, с 1981 по 1987-й руководил Минстанкопромом). – Нынешнее печальное состояние технопарка – большая беда экономики. Немалую часть этого парка надо бы давно сдать в утиль…
Даже в такой передовой отрасли, как космическая промышленность, многие заводы заполнены станками, выпущенными 20–25 лет назад. Это относится и к легендарному предприятию в подмосковном Королеве – Ракетно-космической корпорации «Энергия». Здесь по идее должно использоваться не просто новейшее оборудование, а технологии завтрашнего дня. Ведь корпорация – форпост в будущее, флагман космической отрасли.
– С тяжелым чувством покидал я недавно завод экспериментального машиностроения, входящий в РКК «Энергия», – продолжает Борис Владимирович. – Когда-то здесь создавался первый спутник Земли, гагаринский «Восток», сегодня строят корабли «Союз», на которых космонавты прибывают на Международную орбитальную станцию и затем возвращаются на Землю. Мне хорошо известно это предприятие, много раз бывал здесь в 1960–1980-е годы, когда работал в Министерстве общего машиностроения и позже в Минстанкопроме. Непосредственно участвовал в реализации программ технического обновления производства… И вот сегодня иду по знакомым цехам завода, ищу приметы нового времени. Увы! Вижу те же станки, только сильно изношенные, приобретение которых мы с бывшим генеральным директором «Энергии» Вахтангом Дмитриевичем Вачнадзе согласовывали в инстанциях и закупали для завода в 80-х годах прошлого века. Такого старого оборудования, как мне представляется, здесь не менее 85%. А это ведь не музей, здесь верфь нынешних и будущих космических кораблей. Ситуация, прямо скажу, чрезвычайная. Как бы не оказаться нам окончательно у разбитого корыта. Ведь «Энергия» – особое, знаковое предприятие, играющее исключительно важную роль в отрасли. Пока оно живо, будет развиваться и российская космонавтика…
Тревогу экс-министра разделяют многие работники отрасли. Они сетуют: сейчас не принято говорить о техническом отставании, и реальное положение ускользает от внимания общественности. Вот, например, по телевидению показывают красивые съемки стартующих ракет. Зрителям кажется, что все у нас замечательно, страна идет от одной космической победы к другой. И только посвященные знают, какие острейшие проблемы остаются за кадром. Современного промышленного оборудования, которое эксплуатируется менее пяти лет, в космической отрасли менее 7%. Можно лишь удивляться, как на такой позавчерашней технике удается изготавливать и даже модернизировать пилотируемые «Союзы»…
Но если в таком тяжелом положении оказалась одна из самых передовых отраслей, то каков технический уровень оборудования, оснастки на предприятиях машиностроения, электронной, судостроительной промышленности, в других сферах экономики? Статистическая служба публикует данные или в целом по промышленности, или в лучшем случае по крупным секторам экономики, но почему-то в тайне держит соответствующие оперативные данные по отраслям.
По мировым критериям промышленное оборудование надо менять каждые 6–7, максимум 10 лет. Причем независимо от степени износа станка или обрабатывающего центра. Потому что моральное старение наступает гораздо раньше физического разрушения. Тем не менее у нас нередко пытаются эксплуатировать не только 15–20-летнее, но даже полностью изношенное, давно выработавшее свой ресурс оборудование. Таких станков, машин, механизмов в стране сотни тысяч. Не случайно появились фирмы, которые ремонтируют, меняют приводы станков, реанимируют вышедшие из строя агрегаты. Но на этом подлатанном оборудовании, конечно же, невозможно догнать США или Канаду по производительности труда, не говоря уж о качестве продукции (см. таблицу 1).
Таблица 1. Состояние оборудования, машин, механизмов на крупных и средних российских предприятиях (данные Росстата)
Степень износа, % |
Удельный вес полностьюизношенных машин и оборудования |
||
2004 г. |
2007 г. |
|
|
В среднем |
55,4% |
51,2% |
22,8% |
Обрабатывающие производства (машиностроение, металлургия, металлообработка и т. д.) |
55% |
49,6% |
21,1% |
Добыча полезных ископаемых |
51,4% |
54,8% |
23,8% |
Строительство |
49,4% |
49,3% |
16,7% |
Как видим, станки, механизмы, другое оборудование изношены в среднем на 50%. А у каждого пятого агрегата ресурс выработан до предела, это рухлядь, почти металлолом. Причем ситуация за три года улучшалась черепашьими темпами. Что же касается сферы добычи полезных ископаемых, то здесь положение по сравнению с 2004 годом даже ухудшилась.
Кто приукрашивает положение?
Износ износом, но все-таки каков в стране объем устаревшего оборудования, выпущенного более 10 лет назад? Таких свежих данных, характеризующих всю экономику, в официальных материалах найти невозможно. Но есть оценки Росстата и независимых экспертов по отдельным отраслям. Начнем с документов Федеральной службы государственной статистики. В конце прошлого года в 79 регионах было проведено обследование предприятий в нескольких секторах экономики: обрабатывающая промышленность, добыча полезных ископаемых, производство и распределение электроэнергии, газа, воды. Вот результаты (см. таблицу 2).
Таблица 2. Возраст промышленного оборудования
Машины и оборудование |
|
До 3 лет |
5% |
От 3 до 5 лет |
8% |
От 5 до 10 лет |
21% |
От 10 до15 лет |
26% |
От 15 до 20 лет |
18% |
От 20 до 30 лет |
14% |
От 30 лет |
3% |
Судя по результатам опроса, только треть производственного оборудования можно считать (да и то нередко с большой натяжкой) пригодной для работы в нынешних условиях. А самый важный вывод таков: две трети оборудования – явно устаревшая техника (эксплуатируется более 10 лет). Впрочем, реальная ситуация, возможно, еще хуже. По данным Министерства промышленности РФ, озвученным год назад на заседании правительственной комиссии по развитию промышленности, транспорта и технологий, «средний возраст более 50% парка механообрабатывающего оборудования составляет 20 лет и более».Но опрос, проведенный Росстатом, показывает, что у нас менее трети 20-летних станков и механизмов. Может, работники предприятий, отвечая на анкету статистиков, попросту приукрашивали положение дел?
О тяжелой ситуации в машиностроении с тревогой говорил на очередном заседании правительственной комиссии в декабре прошлого года вице-премьер Сергей Иванов: «Подавляющее большинство – почти 75% станков – имеют возраст от 15 до 20 лет, они уже давно устарели и физически, и морально. Современного же оборудования, работающего менее 5 лет, у нас всего 5%». Комментарии, думаю, не требуются. Между прочим, в малом бизнесе (для которого характерна гибкость, умение быстро перестраиваться, приспосабливаться к новым условиям) ситуация значительно лучше. Здесь, как показал тот же опрос Росстата, половина оборудования не является устаревшим. Только 7% станков эксплуатируется более 20 лет.
Диагноз один: оборудование безнадежно устарело
Для анализа ситуации в конкретных отраслях пришлось привлечь независимых экспертов. Вот их данные (см. таблицу 3).
Таблица 3. Доля устаревшего оборудования в отраслях (экспертные оценки)
Машиностроение и металлообработка – 61%
Судостроение (гражданское) – 63%
Электронная промышленность – 56%
Электроэнергетика – 65%
Черная металлургия – 49%
Химическая и нефтехимическая промышленность – 62%
Промышленность в целом – 62%
Невеселая картина. Что можно, к примеру, ждать от работающей на старой технике отечественной электронной промышленности? Не случайно экономика ощущает острую нехватку современной отечественной электронной продукции. Очень плохо с «элементной базой» – печатными платами, электронными модулями, высокоточными компактными приборами новейшего поколения… Многие предприятия формально выпускают электронную продукцию, но она не соответствует мировому уровню. Поэтому Россия (как в прошлом и СССР) вынуждена покупать эти изделия за рубежом. Но здесь мы идем на немалый риск: а если в компьютерах, платах заложены тайные программы, которые в час икс будут специальной радиокомандой активированы?
Устаревшим оборудованием оснащены и многие предприятия судостроения. В материалах Министерства промышленности, подготовленных для министра Христенко в ноябре прошлого года, содержатся крайне негативные характеристики отрасли: «Критическое научно-техническое отставание от развитых стран. Производственное оборудование, возраст которого превышает 10 лет, составляет 65%. Удельная трудоемкость производства в отрасли в 3–5 раз выше, чем за рубежом; продолжительность постройки судов в 2–2,5 раза больше». В лесной промышленности, а также в текстильной технологический уровень оценивается лишь в 20% от мирового. Примеры можно продолжать…
Станков выпускаем в 25 раз меньше, чем в Советской России
Если кто помнит, в 1970–1980-х годах наша страна занимала передовые позиции в мировом станкостроении. Конечно, Советский Союз не догнал, например, Японию, где еще 40 лет назад мне во время журналистской командировки довелось увидеть впечатляющий, полностью автоматизированный сборочный цех на автомобильном заводе. Однако многие другие страны мы обошли. Освоили выпуск станков с числовым программным управлением, производство перенастраиваемых модулей, обрабатывающих центров и промышленных роботов. В 1975-м было выпущено 128 тыс. металлорежущих станков, из них 4100 – с числовым программным управлением (ЧПУ). Для сравнения: в прошлом году в России произведено металлорежущих станков в 25 раз меньше (лишь 5 тыс.), а с ЧПУ – всего 334. Средний возраст оборудования составлял в СССР в лучшие годы 9 лет, а сегодня в разных отраслях – от 16 до 20 лет.
Казалось бы, достигли неплохого уровня, можно бы и передохнуть. Но страна продолжала наращивать темпы в станкостроении, от которого во многом зависит развитие всей экономики. Каждый год создавалось более 100 моделей новых металлообрабатывающих станков, прессов, соответствующих мировому уровню. В 80-е годы заложили строительство новых заводов в Москве, Ленинграде, Новосибирске… Совместно с японской фирмой «Фанук» начали производство промышленных роботов. Вообще совместным предприятиям открыли тогда «зеленую улицу» – появились компании, работающие с фирмами Швейцарии, Швеции, ГДР, ФРГ… Экспортировали оборудование во многие страны. Поставки шли, разумеется, и на наши заводы. В цехах появлялись роботы, современные автоматические линии…
Рассказ экс-министра можно дополнить впечатляющими статистическими данными. В 1990-м на предприятиях РСФСР работало более 150 тыс. станков с числовым программным управлением (сегодня такого оборудования в возрасте до 14 лет около 3 тыс., или в 50 раз меньше), и в том году страна занимала третье место в мире по производству механообрабатывающего оборудования (после Германии и Японии) и второе место – по его потреблению. Общий парк металлорежущих станков, кузнечно-прессовых и других машин составлял тогда только в РСФСР 2,5 млн. (а всего в СССР было 5 млн.). Нынче от того изобилия осталось 1,5 млн. единиц, причем 1 млн. – устаревшая техника. В лихие 90-е годы заводы останавливались, автоматические линии растаскивали, сдавали в металлолом. «Больно было видеть эту вакханалию», – признается Борис Бальмонт. В период развала экономики станкоинструментальная промышленность рухнула в такую яму, выбираться из которой будет нелегко. О глубине падения свидетельствуют оценки экспертов: по техническому уровню производства в 2005 году Россия находилась на 55-м месте в мире.
Вопрос национальной и экономической безопасности
Понимают ли власти серьезность ситуации? Если судить по официальным заявлениям, понимают. Каждый год проходят посвященные указанным проблемам заседания правительственной комиссии, совещания на разных уровнях. Высокие руководители ставят правильные задачи, чиновники разрабатывают концепции и стратегии, принимают объемные документы, намечают очередные рубежи. И что же? Прорыва нет, выпуск металлорежущих станков в 2007-м сократился, похоже, пар уходит в свисток.
«Годовая потребность российской промышленности составляет не менее 50 тыс. единиц нового механообрабатывающего оборудования, – говорится в служебных материалах Минпрома. – Эта цифра рассчитана, исходя лишь из простого воспроизводства: столько нужно, чтобы сохранить сегодняшний уровень машиностроительного производства». Но задача ведь не в сохранении нынешнего недопустимо низкого уровня, надо энергично двигаться вперед. И по расчетам авторитетных экспертов, для преодоления отставания требуется заменять ежегодно как минимум 100 тыс. устаревших станков, прессов и другого оборудования. Такие масштабы, кстати, были реализованы в советской России еще три десятилетия назад. А для нынешней России это остается несбыточной мечтой. Указанной продукции у нас выпускается лишь 13% от необходимого.
В Германии, где на большинстве предприятий возраст оборудования сравнительно небольшой – 8–9 лет, каждый год заменяют 14% основных фондов. Темпы обновления в два с лишним раза выше, чем в России, заводы которой действительно нуждаются в тотальной модернизации. Таким образом, наше технологическое отставание продолжает увеличиваться. Когда-то мы были среди мировых лидеров, а сегодня вынуждены покупать за рубежом тысячи и тысячи станков, потому что российские предприятия не в состоянии изготавливать аналогичную продукцию на таком высоком уровне. По данным Минпрома, импортная зависимость России в этой сфере достигла в 2006 году опасных масштабов – 87%.
Ситуация осложняется тем, что за рубежом начинают ограничивать продажу новейшей техники, особенно используемой в технологиях двойного назначения. «К этим технологиям, – говорится в министерской аналитической записке, – отнесены все виды оборудования, обеспечивающие производство летательных аппаратов, судов, другой стратегически важной продукции: пятикоординатные обрабатывающие центры, прецизионные станки, станки для объемной лазерной резки… Большая часть механообрабатывающего оборудования, внесенного в эти списки, не производится в нашей стране или серьезно уступает зарубежным аналогам. Российская промышленность будет находиться под угрозой потери доступа к передовой технике. Вот почему наше машиностроение, безусловно, должно быть обеспечено отечественным механообрабатывающим наукоемким оборудованием, относящимся к технологиям двойного назначения. Это вопрос национальной и экономической безопасности».
Иными словами, от замены устаревшего оборудования новым зависит не только повышение производительности труда, но и более серьезные вещи. Почему же столь нужные решения, стратегии, концепции не претворяются в жизнь, лишь умножая бумажные бюрократические пирамиды? Да потому что одних слов, грозных команд, решений мало. От государства требуется система действенных, эффективных мер, в том числе, разумеется, и соответствующие ассигнования.
Речь идет, например, о создании максимально благоприятных условий для организации научно-исследовательских и опытно-конструкторских центров на приоритетных направлениях, чтобы ликвидировать технологическое отставание отрасли. Это может быть частно-государственное партнерство, позволяющее привлечь ученых, конструкторов, бизнес-структуры, без которых трудно будет выпускать конкурентоспособную продукцию. Вклад государства – выделение зданий, покупка всего необходимого для лабораторий, опытных цехов, другие капвложения. Все это надо делать быстро. В стране острейший дефицит национальных технологических ноу-хау. Доля России на мировых рынках высокотехнологичной продукции, по данным Минэкономразвития, всего лишь 0,2%. Мы занимаем 120-е место в мире по цитированию в расчете на одну научную публикацию. А ведь без помощи науки поднять станкоинструментальную отрасль невозможно.
Необходимо также создать мощные стимулы, которые сделают выгодной покупку предприятиями отечественного механообрабатывающего оборудования. Это могут быть солидные налоговые льготы, безвозмездные ссуды, гарантированные госзаказы…
Наконец, государству по силам произвести масштабные закупки новейшего импортного оборудования, которое пока не выпускается в России. «Сейчас, в условиях мирового экономического кризиса, для этого самое лучшее время, – говорит экс-министр Борис Бальмонт. – Разоряющиеся зарубежные фирмы скоро начнут продавать современную технику по супернизким ценам. Этим надо воспользоваться. Образно говоря, покупать не рыбу, а удочку, то есть новые производства, которые позволят нам сделать рывок вперед. Подчеркну: речь идет о приобретении не просто станков и машин, а передовых технологий».
Перечень мер этим, конечно же, не исчерпывается. Во многих документах содержатся детально проработанные предложения. Нужна лишь политическая воля, умелая организация и решимость потратить на реализацию программы не такие уж большие деньги – по расчетам, около 8 млрд. долларов до 2015 года. Когда речь идет о будущем страны, это весьма умеренная плата.
Старый «запорожец» не разгонится до
В начале нынешнего года Владимир Путин, тогда еще президент страны, выступая на заседании Госсовета, поставил задачу: увеличить производительность труда за 12 лет в 4 раза. Но если машиностроительная база останется на таком же архаичном уровне, как сегодня, эта цель будет недостижима в принципе. Потому что на старом «Запорожце», как его ни полируй, невозможно развить скорость
Таблица 4. Рост производительности труда (в % к предыдущему году)
2003 г. |
|
|
В целом в экономике |
+ 7% |
+ 7,1% |
Обрабатывающие производства |
8,8% |
6,3% |
Сельское и лесное хозяйство |
6% |
5,6% |
Добыча полезных ископаемых |
9,2% |
2,3% |
Таблица показывает: не то что 12,5, а даже 8% ежегодного роста производительности труда нашей экономике сейчас не по силам. Необходимость быстрейшего перехода на инновационную модель развития очевидна. Но без активного участия государства, без должного финансирования, продуманных организационных мер задачу не решить. Это становится особенно актуальным в условиях мирового финансово-экономического кризиса, затронувшего и Россию.
По ряду направлений Россия находится в технологической зависимости от ведущих стран мира. В 2007 году число предприятий, осуществляющих технологические инновации, составило в нашей стране лишь 8,5%. Для сравнения: в Великобритании, Финляндии, Франции, Италии, Корее – от 40 до 50%; в Германии этот показатель достигал 73%.
(Из материалов Концепции долгосрочного социально-экономического развития Российской Федерации)
КАК МЫ ДЕЛАЛИ СТАНОК ДЛЯ ЯПОНИИ
Борис БАЛЬМОНТ, с 1981 по 1987-й год руководил Минстанкопромом:
– Еще в 1970 году мировой сенсацией стало изготовление для Японии уникального станка на Коломенском заводе. Фирма «Хитачи» долго искала, кто возьмется за выполнение необычного заказа. Ей требовался карусельный станок, который смог бы обрабатывать детали машин диаметром до
Работа по проектированию и изготовлению этой махины с заводским индексом КУ-299 шла в две, а нередко и в три смены, то есть круглосуточно. Справились за два года. Когда станок смонтировали и запустили в Японии, тамошние инженеры не смогли сдержать эмоции и долго рукоплескали творению наших конструкторов. А потом вице-президент японской торговой ассоциации металлорежущих станков Сюдзю Ямато заявил журналистам: «Советский Союз сделал большой шаг вперед в области экспорта металлорежущего оборудования, особенно крупных карусельных станков. Здесь особенно хочу выделить уникальный КУ-299. По производству станков этого типа СССР вышел на первое место в мире».
Автор: Виталий ГОЛОВАЧЕВ